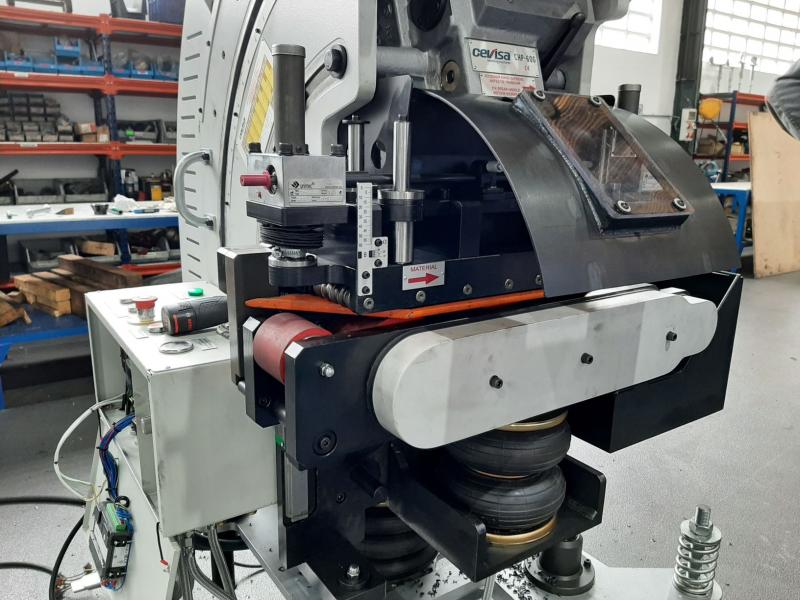
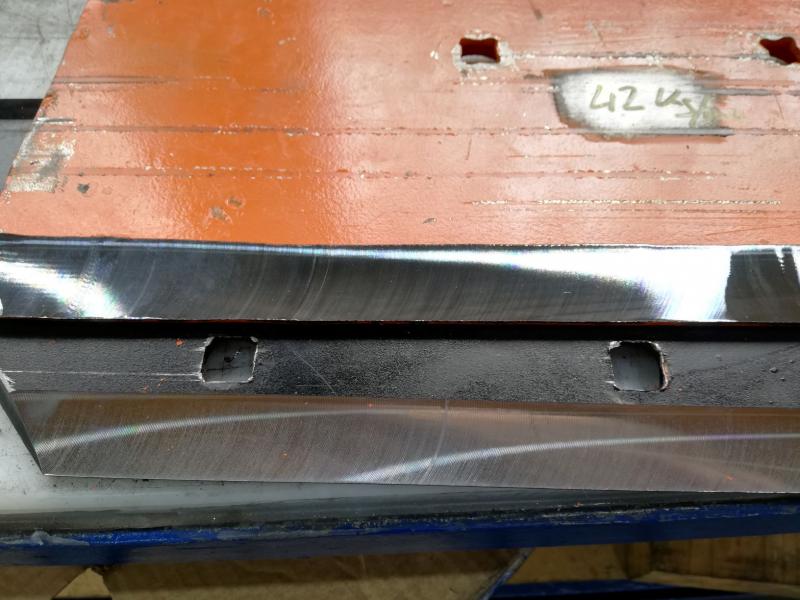
The Basque company Castellanos y Echevarria - Vitoria, S.A., has successfully completed the test series for a new application. This time the request for a demonstration comes from the Portuguese agricultural sector and it concerns the production of cutting edges of the plow blades. The test was carried out with our CHP 60G bevelling machine at an angle of 72º, the materials were different, but given the requirements of the product, all with high durability.
“We receive more and more inquiries that are not used for welding preparation. We learn from the challenges we are faced with, which makes our work so interesting. We did not know this application for the agricultural sector before, but we are very happy to be able to offer a solution in this area. "
Rotary plow blades have a high frequency of wear losses to which they are exposed. They are used both in tractor-operated machines and in small machines (tiller). The rotary plows (Rotavator, rotary harrow and power hoe) are turning tools that break, cut and mix the soil profile. They consist of a rotor that is equipped with blades that are activated by the power take-off of the tractor (with the exception of the hoe, which is driven by its own motor), so that they break and mix the soil in a single pass and mix it for provide the plants.
One of the most serious problems using rotary plows is the break of the blades when they collide with stones and / or hard floors. To avoid this problem, several systems are used that dampen the impact of the blades and protect them from overloads (e.g. couplings). Handling this class of tillage equipment requires technical understanding; The use and operation of rotary plows is very complex, so when defining their use, a thorough study must be carried out before they are introduced into a particular soil. Grinding wear is one of the main causes of failure and loss of performance of rotary plows, as the blades come into permanent contact with hard or abrasive particles under heavy use and cause plastic deformation of the material and detachment.
Steels, which are the basic material for agricultural tools, have different levels of wear resistance depending on the microstructure and chemical composition. For example, martensite generally has higher abrasion resistance than ferrite-pearlite and ferrite carbides as long as the operating conditions do not contain high impact components. A material that has been used successfully for agricultural tools is AISI 15B30 boron steel due to its advantageous combination of toughness and wear resistance. In addition, boron increases the hardenability of hypoeutectoid steels by delaying the nucleation of ferrite at the austenitic grain boundaries.